Trinc Static Eliminator Products
Thank you for your interest in TRINC’s high-quality industrial ionizers!
Below we have listed many case studies to show how our ionizers have reduced dust and contamination problems in paint booths, clean rooms, pharmaceutical facilities, and other applications.
For any questions about your anti-static needs, please feel free to contact us!
Case Studies
Cellular Phone Assembly Process
Dust particle defects reduced by 21%
The assembly lines for cellular phone lenses were facing dust related problems during the manufacturing process. They have used fan type ionizers in the past but after the introduction of TRINC’s desktop ionizer, defects reduced by 21%. TRINC’s air-less technology was the determining factor for their purchase.
Cellular Phone Assembly Line
Drastic drop in dust related defects
The assembly line was using conventional fan-type ionizers for their cell phone touch screen panels. However, once they tested TRINC’s air-less bar ionizer, the defect rate dropped significantly. Now they use TRINC’s ionizer for all their lines.
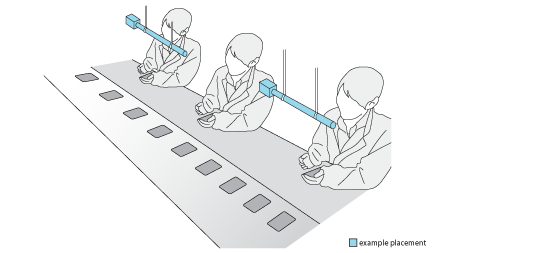
Copier Manufacturing Plant
100% Reduction in complaints
On average, manufacturers will receive 5 complaints every month regarding dust particle defects. However, when TRINC’s space ionizer was introduced to one assembly line, dust particles were kept from sticking to the product and complaints were eliminated. Employees of the assembly line said “We tried many times to blow off the dust, but it never came off this easy before”. They now use the same ionizer in their plant in China.
Glass FPD Factory
Defects Reduced By 80%
Panels attract dust when unpacked and placed on a process line or in between different assembly lines which lowers the yield rate. The lines are isolated from the outside air by transparent acrylic covers, but dust particles still finds a way to attach to the panels. By ionizing the glass substrates and inactivating dust particles, one factory recorded a 75% reduction in defects beginning the next day.
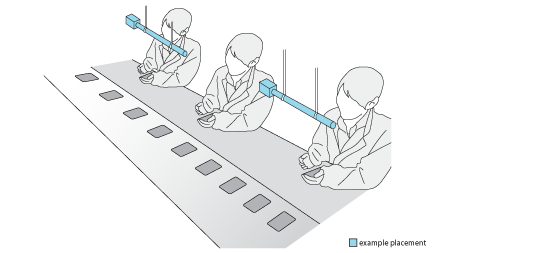
FPC (Flexible Printed Circuits) Manufacturing Plant
Defects reduced by 50%
In a manufacturing factory in China, they previously used a conventional fan type ionizer, but could not stop product defects from occurring. They have replaced their fan type ionizer with TRINC’s space ionizer and reduced their defect rate by half. Now space ionizers are being used throughout the company including factories in Vietnam and Japan.
Polarizing Plate Manufacturing Plant
Defects Reduced By 72%
At the production plant for LCD Polarizing Plates, the debris produced during the process of blanking out the plastic boards was adhering to the products and increasing production defects. Since both the debris and products are plastic, static electricity was generated intensely and no useful countermeasures had been found. However, after introducing TRINC’s bar ionizer into the blanking process, and the space ionizer being installed to cover the whole process, the debris adherence was reduced drastically, and the related defects have been reduced by 72%.
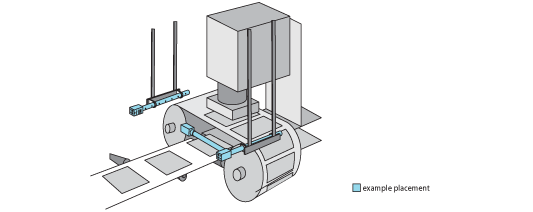
Static Eliminators
LAS-20GL Gun Ionizer Series
Static Eliminators
Desktop Ionizers